Mantener la maquinaria pesada en óptimas condiciones no es solo una opción, sino una necesidad crucial que puede determinar la diferencia entre el éxito y el fracaso de cualquier operación industrial. Las estadísticas demuestran que el 70% de las fallas en equipos pesados son completamente prevenibles con un mantenimiento adecuado.
Sin embargo, muchos operadores y empresas subestiman la importancia de un programa de mantenimiento integral. Por lo tanto, hemos creado esta guía completa que abarca desde las inspecciones diarias fundamentales hasta las últimas tecnologías de diagnóstico, asegurando que tu maquinaria pesada funcione de manera eficiente durante todo el año.
En esta guía, exploraremos estrategias probadas, cronogramas de mantenimiento específicos por temporada y herramientas esenciales que necesitas para maximizar la vida útil de tu equipo. Ya sea que administres una pequeña flota o un gran parque de maquinaria, encontrarás información valiosa para optimizar tus operaciones.
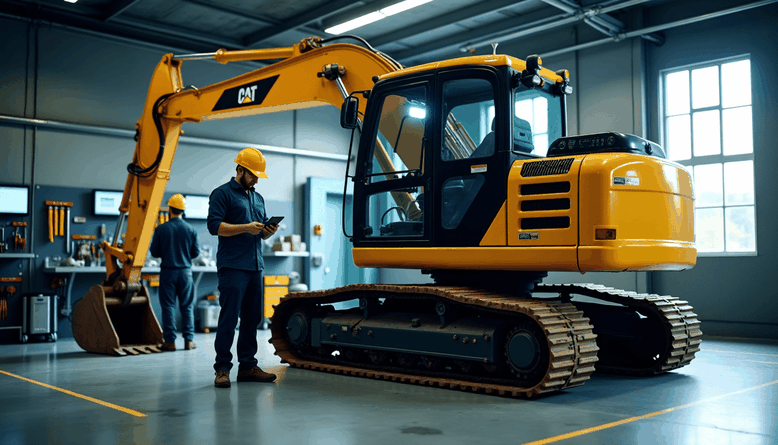
Fundamentos del mantenimiento preventivo de maquinaria pesada
El mantenimiento preventivo representa la columna vertebral de cualquier programa de gestión de maquinaria pesada eficiente. Este enfoque sistemático garantiza la detección temprana de problemas potenciales antes de que se conviertan en averías graves.
Por qué el mantenimiento preventivo es crucial
El mantenimiento preventivo actúa como un escudo protector para tu inversión en equipos. Por consiguiente, las empresas que implementan un programa de mantenimiento preventivo experimentan una reducción significativa en el tiempo de inactividad no programado. Además, este enfoque proactivo mejora la seguridad laboral, asimismo, aumenta la eficiencia operativa y prolonga la vida útil de los equipos.
Los beneficios económicos son igualmente notables. Las estadísticas demuestran que un programa de mantenimiento preventivo bien ejecutado reduce los costos de reemplazo de piezas y optimiza la administración del inventario. Asimismo, las empresas que mantienen sus equipos en óptimas condiciones a través del mantenimiento preventivo pueden mantener las garantías del fabricante activas.
Componentes básicos a revisar
Un programa efectivo de mantenimiento preventivo para maquinaria pesada debe incluir la inspección regular de:
-
Sistemas de combustible y suministro
-
Niveles de aceite del motor y fluido hidráulico
-
Sistema de frenos y neumáticos
-
Refrigerante del motor y sistema de enfriamiento [2]
-
Sistema eléctrico y componentes electrónicos
Frecuencia recomendada de inspecciones
La frecuencia de las inspecciones debe seguir un calendario estructurado. Las revisiones diarias o por turno son fundamentales para identificar problemas potenciales de manera temprana [3]. Por otra parte, las inspecciones trimestrales deben enfocarse en evaluar el estado de las vías de tránsito y áreas operacionales [4].
El mantenimiento programado debe realizarse según las especificaciones del fabricante, considerando las horas de uso o el kilometraje acumulado [1]. Por consiguiente, es esencial mantener registros precisos de cada inspección y servicio realizado, lo que permite anticipar el momento adecuado para el reemplazo de componentes [5].
Inspecciones diarias esenciales
Las inspecciones diarias constituyen el primer nivel de defensa para mantener la maquinaria pesada en funcionamiento seguro y eficiente. Estas revisiones sistemáticas identifican y abordan irregularidades antes de que se conviertan en problemas mayores [6].
Lista de verificación pre-operación
La inspección pre-operacional requiere un enfoque metódico y detallado. Por consiguiente, antes de encender cualquier equipo, los operadores deben realizar una revisión exhaustiva que incluye:
-
Revisión visual completa del equipo en busca de daños estructurales y fugas
-
Verificación de niveles de fluidos (aceite, refrigerante, combustible)
-
Comprobación de sistemas eléctricos y luces
-
Inspección de neumáticos y sistema de frenos
-
Evaluación de controles operativos y mandos [6]
Además, es fundamental documentar cada inspección realizada, incluyendo fecha, hora y detalles específicos de las observaciones [7]. Esta documentación sistemática permite establecer un historial confiable del estado del equipo.
Puntos críticos de control
Los puntos críticos de control (PCC) requieren atención especial durante las inspecciones diarias. Asimismo, estos componentes son especialmente vulnerables y su fallo puede ocasionar consecuencias significativas [8]. Entre los elementos más críticos se encuentran:
Las mangueras y cañerías hidráulicas merecen especial atención, pues su deterioro puede provocar derrames y contaminar el entorno [8]. Por otra parte, el sistema de combustible y los componentes de seguridad deben mantenerse en óptimas condiciones para garantizar una operación segura.
La supervisión periódica de estos puntos críticos facilita el seguimiento detallado de la operación, permitiendo detectar cualquier desviación antes de que afecte el rendimiento del equipo [7]. Por consiguiente, cada observación debe registrarse con precisión, incluyendo evidencia fotográfica cuando sea posible [7].
El monitoreo constante de estos elementos no solo protege la integridad del equipo, sino que también contribuye significativamente a la seguridad del operador y la eficiencia operativa [9]. Además, un sistema de seguimiento bien implementado permite programar mantenimientos de manera eficiente, evitando interrupciones no planificadas en la operación [9].
Sistema de seguimiento y documentación
Un sistema robusto de documentación constituye el pilar fundamental para mantener la maquinaria pesada en funcionamiento óptimo. La documentación precisa y sistemática permite tomar decisiones informadas y anticipar necesidades de mantenimiento.
Registro digital vs manual
Los métodos tradicionales de registro manual, aunque familiares, presentan limitaciones significativas. Por ejemplo, la gestión con papel o hojas de cálculo básicas dificulta la organización y búsqueda de información relevante [10]. En cambio, los sistemas digitales modernos ofrecen ventajas sustanciales, permitiendo la digitalización de órdenes de trabajo, planos y programación de mantenimiento en una plataforma centralizada [11].
La implementación de un software especializado facilita la generación de informes detallados y el seguimiento de indicadores clave como tiempos de respuesta y finalización de órdenes de trabajo [11]. Además, estos sistemas garantizan la seguridad de los datos mediante copias de respaldo automáticas [12].
Datos importantes a documentar
Para mantener la maquinaria en óptimas condiciones, resulta esencial documentar:
-
Fecha y detalles específicos de cada mantenimiento realizado
-
Especificaciones técnicas del servicio ejecutado
-
Piezas reemplazadas y su información de garantía
-
Programación del próximo mantenimiento [13]
Asimismo, cada registro debe incluir la identificación del técnico responsable y un campo de observaciones para notas específicas [14]. La documentación detallada facilita la tramitación de garantías y permite crear programas de mantenimiento especializados.
Análisis de tendencias
El análisis de tendencias mediante Maintenance Analytics permite identificar patrones y anomalías en el funcionamiento de los equipos [15]. Esta capacidad analítica avanzada facilita la visualización de datos complejos, permitiendo actuar de manera proactiva para mejorar la eficiencia operativa.
Los algoritmos predictivos, en conjunto con el aprendizaje automático, analizan continuamente los datos para detectar signos tempranos de posibles fallos [15]. Por consiguiente, esta información resulta vital para optimizar los ciclos de mantenimiento y reducir los costos operativos a largo plazo.
El monitoreo en tiempo real de las condiciones operativas proporciona información crucial sobre el estado actual de la maquinaria [15]. Por otra parte, el análisis histórico de datos permite identificar patrones de desgaste recurrentes, facilitando la planificación estratégica del mantenimiento [10].
Mantenimiento por temporada
Las condiciones climáticas cambiantes exigen adaptaciones específicas en el mantenimiento de la maquinaria pesada para garantizar su rendimiento óptimo durante todo el año. Un programa de mantenimiento estacional bien estructurado previene el desgaste prematuro y prolonga la vida útil del equipo.
Preparación para clima cálido
Las altas temperaturas pueden afectar significativamente el rendimiento de la maquinaria pesada. Por consiguiente, es fundamental mantener los sistemas de enfriamiento en óptimas condiciones. Los radiadores y enfriadores deben permanecer limpios y libres de obstrucciones [16].
Durante esta temporada, resulta esencial verificar regularmente el estado de los filtros de aire del motor, estableciendo un intervalo mínimo de 50 horas para su revisión [16]. Además, los fluidos requieren atención especial, pues el calor extremo puede aumentar el desgaste de las piezas mecánicas y componentes eléctricos [17].
Ajustes para temporada de lluvias
Mantenimiento de Maquinaria Pesada en Época de Lluvias: Medidas Clave
La temporada de lluvias exige atención especial en el cuidado de maquinaria pesada para prevenir fallos, corrosión y accidentes. A continuación, se detallan prácticas esenciales para garantizar su óptimo funcionamiento:
Protección Anticorrosiva
La humedad acelera la oxidación en componentes metálicos. Aplique recubrimientos protectores (como grasas o sprays anticorrosivos) en piezas expuestas, especialmente en uniones, tornillería y estructuras de soporte. Inspeccione regularmente zonas críticas como el chasis y verifique que los sellos estén intactos para evitar filtraciones.
Lubricación de Partes Móviles
El agua puede arrastrar lubricantes y contaminar sistemas. Reemplace o rellene fluidos con productos resistentes al agua y asegúrese de que juntas, cojinetes y ejes estén correctamente lubricados. Priorice el uso de grasas de alta adherencia para evitar el lavado por lluvia.
Revisión de Sistemas Eléctricos
La exposición a la humedad genera cortocircuitos y fallas en conexiones. Aísle terminales, baterías y sensores con protectores dieléctricos o cubiertas impermeables. Verifique el estado de los cables y reemplace aquellos con aislamiento dañado.
Limpieza de Zonas Críticas
Tras cada jornada, retire lodo, piedras y residuos acumulados en orugas, ruedas, radiadores y sistemas de ventilación. Estos materiales retienen humedad, obstruyen el flujo de aire y aumentan el peso de la máquina, reduciendo su eficiencia.
Control de Neumáticos y Orugas
En terrenos fangosos, revise la presión de los neumáticos para evitar hundimientos y desgastes irregulares. En equipos con orugas, ajuste la tensión para evitar deslizamientos y verifique que no haya grietas o eslabones dañados.
Drenaje de Combustible y Filtros
El agua puede infiltrarse en el tanque de combustible o lubricantes. Use filtros con separadores de agua y drene los depósitos con frecuencia. Opte por aditivos que eviten la condensación en el sistema de combustible.
Almacenamiento Adecuado
Si la maquinaria no está en uso, guárdela en superficies elevadas y bajo techado. Cubra motores y cabinas con lonas impermeables, pero evite sellarlas completamente para permitir ventilación y prevenir condensación interna.
Inspección Postoperación
Después de trabajar en condiciones húmedas, realice una revisión completa: examine fugas, niveles de fluidos (aceite, refrigerante, hidráulico) y el funcionamiento de frenos y sistemas de seguridad.
Capacitación del Operador
Instruya a los operadores para reportar anomalías como vibraciones inusuales, ruidos extraños o pérdida de potencia, que podrían indicar infiltración de agua en sistemas críticos.
El mantenimiento preventivo en época lluviosa no solo alarga la vida útil de la maquinaria, sino que reduce costos de reparación y riesgos operativos. Adaptar protocolos a las condiciones climáticas garantiza productividad y seguridad en proyectos de construcción, minería o agricultura.
Cuidados en clima frío
El frío extremo exige protocolos específicos de mantenimiento. Las baterías requieren atención especial, pues las bajas temperaturas reducen su capacidad de arranque [18]. Por consiguiente, es fundamental mantenerlas completamente cargadas y limpiar cualquier corrosión en terminales y conectores.
Los fluidos deben adaptarse a las condiciones invernales. El depósito de combustible debe mantenerse lleno para evitar la condensación [18]. Además, resulta crucial utilizar aceites y lubricantes específicos para bajas temperaturas, asegurando una lubricación adecuada de todos los componentes [19].
El sistema de arranque en frío merece especial atención. Los calentadores del motor deben funcionar correctamente para mantener los líquidos a temperatura adecuada [18]. Por otra parte, es fundamental realizar inspecciones regulares del sistema de escape y ventilación para prevenir acumulaciones de hielo que puedan afectar el rendimiento del equipo.
Tecnologías de diagnóstico modernas
Los avances tecnológicos han revolucionado el diagnóstico y monitoreo de la maquinaria pesada, permitiendo una gestión más precisa y eficiente del mantenimiento. Los sistemas modernos de diagnóstico reducen los costos de mantenimiento entre un 5-10% y aumentan el tiempo de actividad del equipo entre un 10-20% [2].
Sistemas de monitoreo en tiempo real
La integración de sensores y sistemas telemáticos permite supervisar constantemente el rendimiento de los equipos. Los datos recopilados por estos sistemas facilitan la detección temprana de problemas potenciales, manteniendo la maquinaria en óptimas condiciones. Según estudios recientes, más del 80% de las empresas de construcción que utilizan telemetría reportan mejoras significativas en la eficiencia operativa, con una reducción promedio del 15% en los costos de combustible [2].
Los sistemas de monitoreo actuales incorporan:
-
Sensores que supervisan componentes críticos
-
Tecnología IoT para transmisión de datos
-
Sistemas de alerta temprana
-
Análisis predictivo de fallos
La capacidad de estos sistemas para capturar e interpretar los Códigos de Problemas de Diagnóstico (DTC) en tiempo real funciona como un sistema de advertencia anticipada [2]. Además, la telemetría permite supervisar ángulos de plumas y la inclinación de las máquinas, aspectos cruciales para la seguridad operativa [2].
Herramientas de diagnóstico esenciales
Las soluciones avanzadas de diagnóstico integran múltiples tecnologías que permiten una evaluación completa del estado de los equipos. Los vehículos modernos, equipados con sistemas electrónicos complejos, requieren herramientas especializadas para identificar y resolver problemas eficientemente [20].
El software de diagnóstico moderno ofrece capacidades como:
-
Lectura de códigos de error en tiempo real
-
Análisis detallado de datos operativos
-
Guías específicas de reparación
-
Monitoreo de emisiones
Los sistemas de diagnóstico actuales desempeñan un papel fundamental en la supervisión de emisiones y el cumplimiento normativo [20]. Asimismo, las plataformas de gestión de flotas complementan estas herramientas al integrar datos de diagnóstico para ofrecer una experiencia de mantenimiento integral [2].
La implementación de estrategias de mantenimiento predictivo, respaldadas por estas tecnologías avanzadas, ha demostrado un aumento del 20% en la Efectividad Global del Equipo (OEE) en comparación con el mantenimiento reactivo tradicional [2]. Por consiguiente, estas herramientas no solo mejoran la eficiencia operativa sino que también prolongan la vida útil de los equipos.
El impacto de estas tecnologías se refleja en la capacidad para recopilar y analizar datos en tiempo real, permitiendo tomar decisiones informadas sobre el mantenimiento y la operación de la maquinaria [21]. Por otra parte, la integración de sensores en la maquinaria facilita la recopilación de datos cruciales para el mantenimiento predictivo, evitando paradas no programadas [21].
Conclusión
El mantenimiento adecuado de la maquinaria pesada representa una inversión estratégica que genera beneficios tangibles a largo plazo. Las estadísticas demuestran que las empresas que implementan programas integrales de mantenimiento logran reducir sus costos operativos hasta en un 30%, mientras aumentan significativamente la vida útil de sus equipos.
La combinación de inspecciones diarias meticulosas, documentación sistemática y tecnologías modernas de diagnóstico establece las bases para una operación eficiente y segura.
Ciertamente, el seguimiento de un programa de mantenimiento estacional garantiza que los equipos funcionen de manera óptima durante todo el año, adaptándose a las diferentes condiciones climáticas.
Los avances tecnológicos en sistemas de monitoreo y diagnóstico han transformado la gestión del mantenimiento, permitiendo anticipar problemas antes de que afecten la productividad. Estas herramientas, junto con un registro detallado y análisis de datos, facilitan la toma de decisiones informadas y optimizan los recursos disponibles.
La implementación exitosa de estas estrategias requiere compromiso y consistencia. Los resultados son evidentes: mayor disponibilidad de equipos, reducción de costos por reparaciones de emergencia y un entorno de trabajo más seguro para los operadores. Sin duda, la inversión en mantenimiento preventivo y tecnologías de diagnóstico modernas representa el camino más efectivo hacia la excelencia operativa en la gestión de maquinaria pesada.
Referencias
[1] - https://cementosanmarcos.com/temporada-de-lluvias-un-desafio-que-podemos-prevenir-y-superar/ [2] - https://www.navixy.com/es/blog/telematica-en-maquinaria-pesada-redefiniendo-la-eficiencia/ [3] - https://www.toyotaforklift.com/es/resource-library/blog/parts-and-service/understanding-forklift-inspection-frequency [4] - https://www.minsur.com/wp-content/uploads/2022/05/MI-COR-SSO-CRI-EST-14-Estándar-Operacional-Vehículos-y-Equipos-Motorizados-Pesados-versión-03.pdf [5] - https://www.cursosaula21.com/mantenimiento-preventivo-tips-lista-verificacion/ [6] - https://www.revei2000.com/blog/inspecciones-maquinarias/ [7] - https://safetyculture.com/es/temas/analisis-de-peligros-y-puntos-criticos-de-control/ [8] - https://es.scribd.com/document/319595189/Puntos-Criticos-de-Equipos [9] - https://blog.persat-latam.com/la-importancia-crucial-de-las-inspecciones-en-maquinaria-pesada/ [10] - https://www.cegid.com/ib/es/blog/ventajas-software-gmao-control-manual-gp/ [11] - https://www.emaint.com/es/industries/equipment-maintenance/ [12] - https://software.aeromarine.es/que-es-un-informe-de-mantenimiento-y-como-asegurar-su-veracidad/ [13] - https://www.maquinariacarran.cl/mantenimiento-maquinaria-pesada/ [14] - https://www.kizeo-forms.com/lat/blog/ficha-de-mantenimiento-de-maquinaria-industrial/ [15] - https://www.fracttal.com/es/blog/futuro-del-mantenimiento-industrial-6-tendencias-2024 [16] - https://salfamaquinaria.cl/tips-para-proteger-del-calor-a-operadores-y-la-maquinaria-pesada/ [17] - https://www.taopparts.com/blog/preparados-para-el-verano-y-tu-maquina-esta-realmente-preparada-para-el-calor/ [18] - https://alquimaq.es/como-cuidar-la-maquinaria-en-invierno/ [19] - https://www.revei2000.com/blog/protege-maquinaria-obra-publica-frio/ [20] - https://es.agridiaginfo.com/diagnostic-des-poids-lourds-un-marche-porteur/ [21] - https://blog.cetemin.edu.pe/innovaciones-en-maquinaria-industrial-nuevas-tecnologias-y-tendencias-en-el-montaje-y-mantenimiento-de-maquinaria-pesada/